印染机械,染色机,液压加压机构
由于液压加压机构是以油压为加压工作介质,因而又称为油压加压机构。如图3-3所示,加压时由齿轮油泵1将油自储油箱2输经稳压器至三向调节阀9,再通过并联管路分别输至下轧液辊两端轴承座下方的加压油缸4、5,推动活塞顶起下、中辊压向位置固定于机架的上辊,自下向上传压。
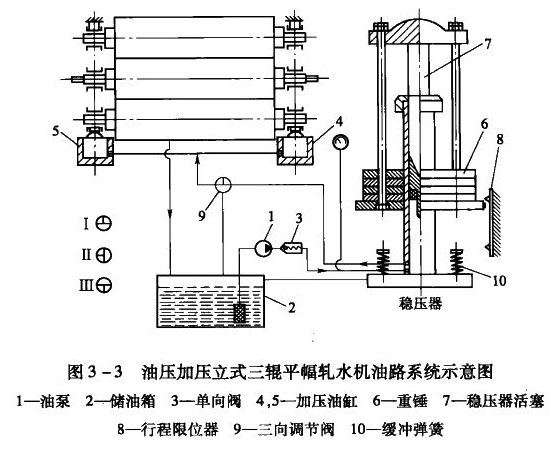
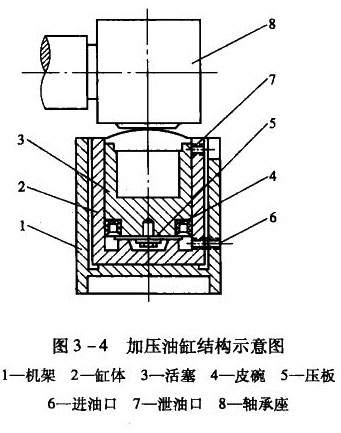
图3—4所示为加压油缸结构图。缸体和活塞都为铸铁件,两者动配合,活塞3下端有环形槽,用压板5将皮碗4固定于槽内。当高压油进入缸体向上推动活塞时,利用被撑开的皮碗压向缸体内壁使两者紧密配合,以防止和减少油。至于泄漏的少量油可自缸体上端的泄油口经回油管路回流到储油箱。
为了改善加压系统油压的稳定性,将三向调节阀9需油压强而加的重锤6及其支架的重力施加于稳压器升降轴心上,使系统内因漏油致使油压下降的数值维持在较小范围内。通过重锤升降行程限位器8,可自动控制拖动齿轮油泵电动机的运转。
为了便于计算,常略去加压系统漏油影响不计,则如图3—3所示的轧水机上下轧点的总压力和线压力可按下式计算:
上轧点总压力P,(N):

下轧点总压力P2(N):

上轧点线压力q1(N/cm)
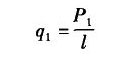
下轧点线压力q2(N/em)
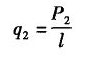
并且:
P1<P2 q1<q2
式中:p为加压系统内油的压强(MPa)A为每只加压油缸的活塞面积(cm2);a为稳压器升降轴心横截面积(cm2);W1、W2分别为中、下轧液辊及其两端轴承、轴承座的重量(N);W3为一只加压油缸的活塞和顶块的重量(N);W4为稳压器升降轴心、重锤及其支架等的重量(N);l为轧液辊的辊面幅度(cm)。
加压油缸活塞的直径视轧水、轧液要求的压力而定,通常为150~200mm。稳压器升降轴心的直径一般为30-50mm。
轧液辊组的加压、卸压是通过三向调节阀变换的。图3—3中,位置I为辊组加压;位置Ⅱ为辊组短时间卸压,系统中的加压油泵和稳压器仍保持工作压强;位置Ⅲ为辊组和稳压器都卸压,用于辊组需较长时间卸压的情况。
油压加压可获得高压,操作控制方便,加压系统较气压加压安全。但因加压油缸漏油,需配置稳压装置稳定油压。为了避免加压油缸漏油沾污辊面和织物,轧液辊组传压方向一般是自下而上,从而需抵消中、下两辊及其轴承、轴承座等的重力后才为有效压力。但曾见到有的进口轧上下杠杆和连杆,将加压油缸活塞向上施压改变为自上向下向轧辊组传压,解决了轧辊组自下向上传压的上述缺陷。
油压加压主要用于轧点线压力较高(500-1500N/m)和加压总压力较大(9.8×104N以上)的设备.如轧光机、电光机、轧纹机和某些丝光碱液浸轧机等。